A Comprehensive Guide to the Refine and Benefits of Plastic Extrusion
In the vast world of manufacturing, plastic extrusion emerges as a highly effective and necessary process. Altering raw plastic right into constant accounts, it satisfies a wide variety of sectors with its impressive convenience. This overview intends to illuminate the elaborate steps associated with this method, the sorts of plastic appropriate for extrusion, and the game-changing benefits it offers the sector. The occurring conversation guarantees to unravel the real-world impacts of this transformative process.
Understanding the Basics of Plastic Extrusion
While it may appear facility at first glance, the process of plastic extrusion is fundamentally straightforward. The process starts with the feeding of plastic product, in the form of powders, pellets, or granules, right into a warmed barrel. The shaped plastic is after that cooled down, strengthened, and cut into preferred sizes, completing the process.
The Technical Refine of Plastic Extrusion Explained

Sorts Of Plastic Suitable for Extrusion
The option of the best kind of plastic is a crucial element of the extrusion process. Various plastics provide special residential or commercial properties, making them more matched to particular applications. Polyethylene, for instance, is commonly utilized because of its reduced price and easy formability. It uses outstanding resistance to chemicals and moisture, making it ideal for items like tubing and containers. Likewise, polypropylene is an additional prominent choice as a result of its high melting point and resistance to tiredness. For more robust applications, polystyrene and PVC (polyvinyl chloride) are often selected for their strength and resilience. Although these prevail options, the selection ultimately depends upon the specific requirements of the item being created. Understanding these plastic kinds can significantly improve the extrusion process.
Contrasting Plastic Extrusion to Various Other Plastic Forming Techniques
Comprehending the kinds of plastic suitable for extrusion leads the way for a more comprehensive conversation on exactly how plastic extrusion stacks up versus various other plastic developing approaches. Plastic extrusion is unmatched when it comes to creating continual profiles, such as pipes, gaskets, and seals. It also permits for a consistent cross-section along the length of the item.
Secret Advantages of Plastic Extrusion in Manufacturing
In the world of production, plastic extrusion supplies lots of significant benefits. One significant benefit is the cost-effectiveness of the procedure, which makes it an economically appealing production approach. Furthermore, this method provides remarkable item flexibility and boosted manufacturing speed, thereby boosting overall production effectiveness.
Economical Manufacturing Method
Plastic extrusion leaps to the center as a cost-effective production method in production. This procedure stands apart for its capacity to generate high quantities of material quickly and successfully, offering producers with substantial savings. The key price benefit is the capacity to use cheaper resources. Extrusion utilizes thermoplastic materials, which are much less costly contrasted to metals or ceramics. Better, the extrusion procedure itself is reasonably straightforward, minimizing labor prices. In addition, plastic extrusion calls for much less power than conventional manufacturing approaches, adding to reduced operational expenses. The procedure also decreases waste, as see here any malfunctioning or excess materials can be reused and reused, providing an additional layer of cost-effectiveness. In general, the financial benefits make plastic extrusion a very eye-catching option in the production sector.
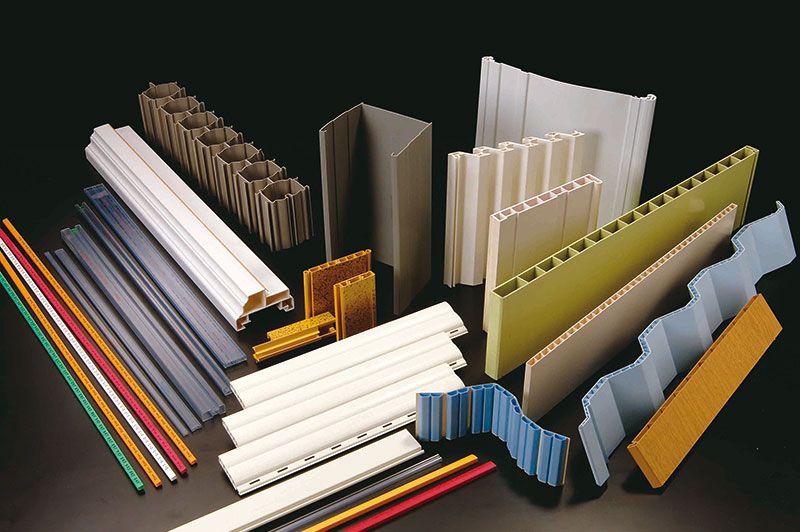
Superior Item Flexibility
Past the cost-effectiveness of plastic extrusion, an additional significant advantage in making depend on its exceptional product adaptability. This process permits for the development of a wide variety of products with differing designs, dimensions, and forms, from basic plastic sheets to elaborate accounts. The flexibility is associated to the extrusion die, which can be customized to generate the desired product style. This makes plastic extrusion an optimal option for industries that need personalized plastic elements, such as automotive, building, and packaging. The capability to generate diverse items is not just helpful in meeting particular market demands however likewise in allowing makers to discover new product with marginal resources financial investment. Essentially, plastic extrusion's product adaptability promotes innovation while boosting operational effectiveness.
Boosted Production Speed
A significant advantage of plastic extrusion hinges on its boosted manufacturing speed. This manufacturing procedure permits for high-volume manufacturing in a fairly brief time period. It is qualified of producing long, continuous plastic profiles, which significantly decreases the manufacturing time. This high-speed manufacturing is specifically useful in markets where big amounts of plastic components are required within tight deadlines. Few various other production processes can match the rate of plastic extrusion. Furthermore, the ability to preserve regular high-speed production without giving up item quality sets plastic extrusion besides other methods. The improved manufacturing speed, as a result, not just allows makers to satisfy high-demand orders but also adds to enhanced efficiency and cost-effectiveness. This helpful function of plastic extrusion has made it a preferred option in many markets.
Real-world Applications and Impacts of Plastic Extrusion
In the realm of manufacturing, the strategy of plastic extrusion holds profound significance. The economic benefit of plastic extrusion, mainly its high-volume and cost-effective outcome, has changed manufacturing. The sector is persistently aiming for developments in biodegradable and recyclable materials, indicating a future where the advantages of plastic extrusion can be preserved without jeopardizing environmental sustainability.
Conclusion
Finally, plastic extrusion is a reliable and very reliable method of transforming basic materials into diverse items. It supplies many advantages over various other plastic forming techniques, consisting of cost-effectiveness, high output, very little waste, and design adaptability. Its impact is greatly felt in various sectors such as construction, auto, and consumer products, making it a crucial process in today's production landscape.
Delving much deeper right into the technical process of plastic extrusion, it begins with the option of the proper plastic product. Once cooled, the plastic is reduced into the required sizes or injury onto reels if the item is a plastic movie or sheet - plastic extrusion. Contrasting Plastic Extrusion to Other Plastic Forming Techniques
Comprehending the try here types of plastic appropriate for extrusion paves the method for a wider conversation on how plastic extrusion stacks up versus various other plastic creating techniques. Few other manufacturing procedures can match the rate of plastic check out here extrusion.